Automatisierung in der Fertigung – Chancen und Risiken für Unternehmen
Die Automatisierung von Arbeitsprozessen findet in größer werdenden Ausmaßen statt. Die deutsche Schwerindustrie soll sich soweit möglich an das von der Bundesregierung unterstützte Referenzmodell Industrie 4.0 halten und damit nicht nur auf computergesteuerte Technik setzen, sondern auf eine globale Vernetzung von Maschine, Software und Mensch mittels des Internets der Dinge.
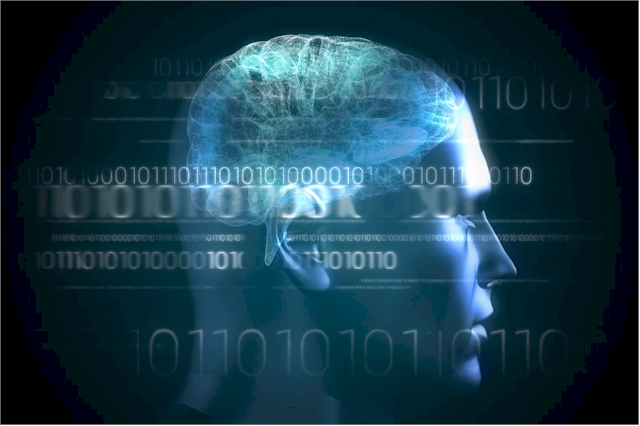
Automatisierung und künstliche Intelligenz gewinnen weiter an Bedeutung
(Foto: wavebreakmediamicro/Clipdealer.de)
Gerade in Fertigung und Logistik gibt es immenses Automatisierungspotential.
Wie bei allen neuen Technologien gibt es jedoch Bedenken, inwiefern die Sicherheit der Systeme gewährleistet wird und ob das erhoffte wirtschaftliche Wachstum auch eventuelle Risiken rechtfertigt.
Risikobeurteilung automatisierter Systeme
Das Herzblut von gemäß Industrie 4.0 automatisierten Prozessen sind Daten. In der Fertigung kommen zur Datenerhebung eine Vielzahl an Mess- und Prüftechniken zum Einsatz, wie optischer Messung, Temperaturmessung, magnetisch-induktive Messungmagnetisch-induktive Messung und sogar Ultraschall. Diese Daten werden interpretiert und zur weiteren Steigerung der Produktivität verwendet. Dieser Prozess ist typischerweise der menschlichen Komponente vorbehalten, aber auch eine Automatisierung der Datenauswertung ist möglich, auf deren Basis selbst das Risikomanagement ver-digitalisiert wird. Hier besteht das Problem, dass mögliche Gefahren erst beurteilt werden, wenn es Präzedenz gibt, d.h. wenn es bereits zu einem Produktionsfehler oder gar einem Unfall gekommen ist. Neben einer extrem umfangreichen Bibliothek an Referenzen kann das automatisierte Risikomanagement also nur reagieren und nicht spekulieren.
Auch die Cybersicherheit spielt eine wichtigere Rolle, sobald ein automatisiertes System in ein Netzwerk eingegliedert wird. Die Lösung für beide Probleme könnte der Einsatz von selbstlernender Künstlicher Intelligenz sein, jedoch steckt diese Technologie noch in den Kindeschuhen und wird derzeit noch weiträumig getestet.
Einschränkung der Flexibilität
Beim Einsatz automatisierter Systeme sind Unternehmen immer mehr von den Herstellern derselben abhängig. Gerade kleinere Firmen verzichten oft auf eigene Ingenieure und Wartungsmannschaften und nutzen stattdessen den Herstellerservice. Dies kann im Zweifel zu längeren Ausfällen führen. Auch wenn bestimmte Teile nicht mehr produziert werden, kann ein Austausch problematisch werden.
Chancen der Automatisierung
Die Vorteile von komplett automatisierten Arbeitsprozessen sind offensichtlich. Besonders repetitive Tätigkeiten wie Fließbandarbeit können in hoher Frequenz und ohne Fehler ausgeführt werden. Mitarbeiter werden so körperlich und psychisch entlastet und die allgemeine Arbeitsqualität steigt. Auch wird die stetig steigende Nachfrage befriedigt und höhere Absatzmengen bedeuten höheren Gewinn. Moderne Automatisierung ist skalierbar und modular, sie kann also ganz den Anforderungen des Unternehmens und seinen Kunden angepasst werden. Viele deutsche Firmen sehen in der Automatisierung ihre einzige Chance, mit ihren globalen Konkurrenten mitzuhalten.
Arbeitsplätze
Die mit Abstand größte Sorge bleibt die Beschäftigung. Eine Automatisierung heißt nicht zwingend einen Arbeitsplatzverlust, aber in jedem Fall einen Strukturwandel. Neben neuen Arbeitsplätzen in der Wartung und Kontrolle der Systeme werden alte, obsolete Arbeitsplätze umgewandelt und gewinnen an Kompetenzen. Dadurch werden sie allerdings auch anspruchsvoller. Das Institut für Arbeitsmarkt- und Berufsforschung rechnet nicht mit einem massiven Arbeitsplatzverlust bis 2030. Es rät jedoch, betroffene Mitarbeiter rechtzeitig zu schulen und auch das Bildungssystem zukunftsfähig zu gestalten, damit nachfolgende Generationen für die sich ständig ändernden Anforderungen am Arbeitsmarkt gewappnet zu bleiben.